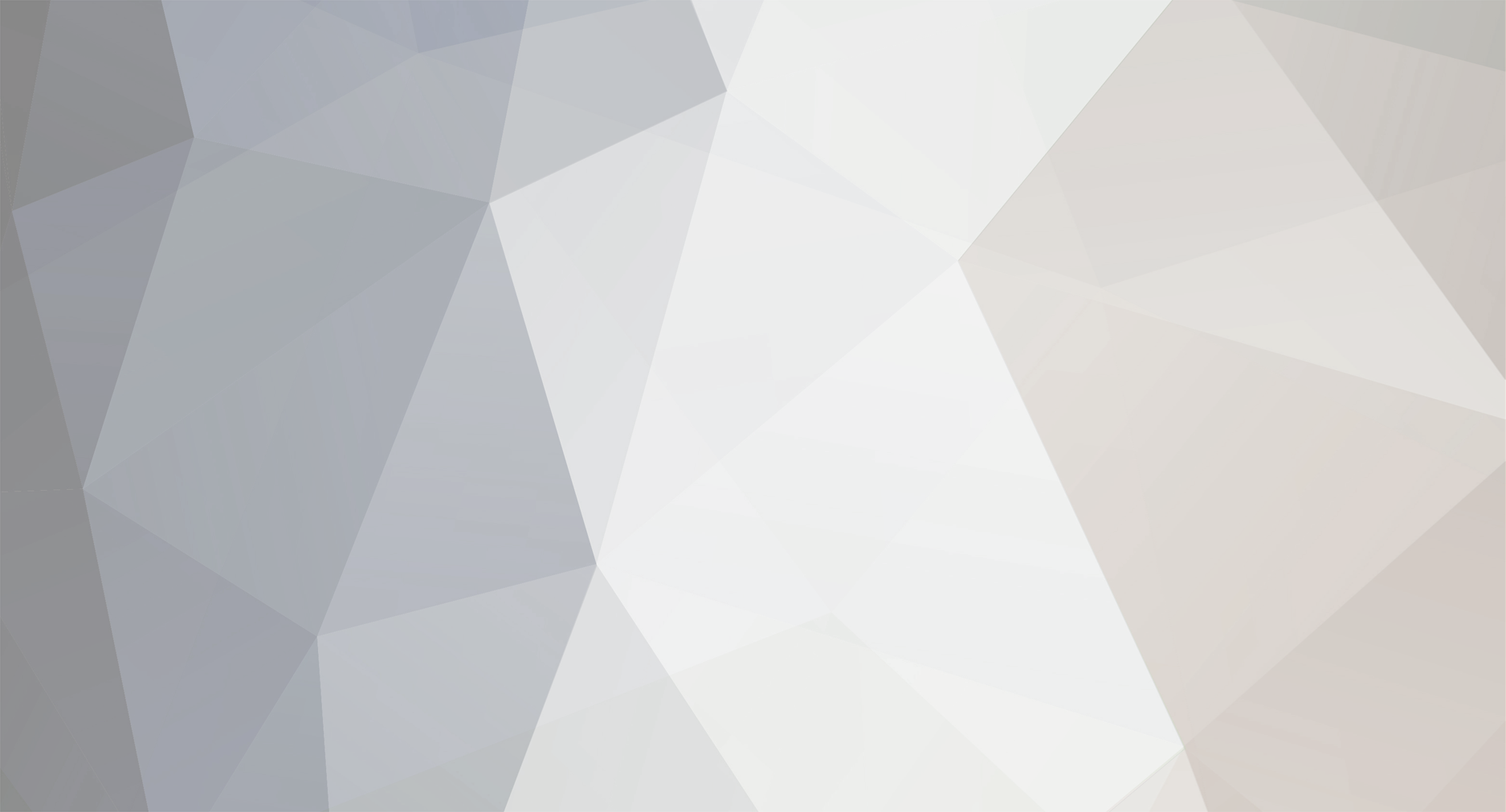
fragarock
501st Pathfinder-
Posts
67 -
Joined
-
Last visited
-
Days Won
2
Everything posted by fragarock
-
Fragarock's Scout Build
fragarock replied to fragarock's topic in Scout Trooper: "The Mandalorian" WIP
I scraped off the TD greeblie with a putty knife, thank God for E6000 comes off easy. Then removed the tab from the top side of the greeblie using my Dremel grinding wheel. A bit of touch-up paint and then glued it right back on. -
Fragarock's Scout Build
fragarock replied to fragarock's topic in Scout Trooper: "The Mandalorian" WIP
Oh, didn't realize that little detail. Easily fixable. Just need to get off the couch. Ow, thats the hard part. Sent from my SM-G960U using Tapatalk -
Fragarock's Scout Build
fragarock replied to fragarock's topic in Scout Trooper: "The Mandalorian" WIP
I have a thermal detonator! Just in time for Christmas. Grabbed some 1.5" diameter gray hose from the pool store and cut the end fitting off of it. I bought a few PVC drain pipe accessories from the local hardware store. The longer piece is 1.5" diameter and I'll use cut sections installed inside the hose as reinforcing where I screw in the belt clips. The smaller bits are 1.5" end fittings and will be used on the ends of the hose to secure the end caps. I cut the PVC pipe lengthwise, not pretty but that's okay. Because it's 1.5" diameter, same as the hose, I need to reduce it's size a bit. Cutting it allows it to be folded in on itself, reducing its diameter so it fits within the hose. I didn't use this whole long piece, I cut it inti (2) 1" wide pieces which I then slipped into hose in the general area where the belt clips would attach. Friction held them in place pretty well. This is the piece inside the hose. Along the hose is a seam. I used this as a straight line reference for placing the clips to ensure they would both be in alignment. I marked each end with a red cross where the bottom screw of the clip would be installed. I then drilled a hole through the hose and into the PVC insert inside. After that, I screwed in the clip through the bottom hole and into the PVC insert inside the hose. Once that was done I put the top screw into the clip. Originally I used #8x3/4" sheet metal screws which is what I had on hand. But these are tapered, meant to be countersunk which wasn't easy to do. They would also create a catch point when trying to clip this onto the belt. Next day I replaced them with pan head screws of the same size which sit flush against the hose. Kinda hard to see in this photo but these are the screws going into the hose and PVC reinforcing. For reference, here's the clip I used which others have recommended. Before installing it, I bent it out a bit as it was too tight and would be hard to slip over the belt fabric. Next step is to insert the PVC end pieces that I purchased. These will pop right into the end of the hose with just a bit of wiggling. They are friction fit into the hose. The flanges on the end provide a good surface for gluing on the ABS end caps onto the hose. The replacement pan head screws. I trimmed the control panel box and drilled a couple holes where the zip tie would come through. Even after trimming the ends of this box piece to received the hose it's still tight. You'll need to align the grooves in the hose with the ends of the box to make it fit better. Then I inserted the zip tie so the clasp was on the back side and gradually tightened it up until the control box seemed snug and wouldn't slide around on the hose. Last part was to put on the end caps. Took a compass to create an even trim line around these pieces. Made them 5/8" tall. These then get glued to the installed PVC pieces on the end of the hose. I used E6000. Last thing was to glue on the control panel greeblies with E6000. These were previously trimmed and painted back when I did the bicep greeblies. That's it for now. I'm working on the knee armor next. -
Fragarock's Scout Build
fragarock replied to fragarock's topic in Scout Trooper: "The Mandalorian" WIP
Am I correct in thinking the knee armor only uses the 1" main elastic strap, not the smaller 1/2" strap or are both acceptable? Didn't see the secondary strap mentioned in the CRL or see it on some of the newer builds although it may have been on some of the first builds when folks converted their ROTJ kits to Mando. Didn't see it in the screen captures from the show either, looks like the 1" strap is above the knee (since the piece is upside down) and holds it in place. THanks -
Fragarock's Scout Build
fragarock replied to fragarock's topic in Scout Trooper: "The Mandalorian" WIP
Success! Local pool store had some 1.5" silver/gray hose. Had to buy 6' of it but it was only $11. Trimmed it to 12" length, will evaluate how it looks proportionally on me and reduce if needed. I'll likely paint this or work on some way to weather it down, it's too new and shiny. -
Fragarock's Scout Build
fragarock replied to fragarock's topic in Scout Trooper: "The Mandalorian" WIP
Thanks Retrofire and Chopper. I wouldn't have caught the subtlety of the flexible hose. I figured it was a generic term being used in the CRL. Gonna hit up my local pool store tomorrow and see what I can find. Also have some clips coming. Will start trimming the plastic parts down while I wait on the other components. -
Fragarock's Scout Build
fragarock replied to fragarock's topic in Scout Trooper: "The Mandalorian" WIP
Made more progress in between work and getting ready for Christmas. First thing I did was go back to the drop boxes and trim off a bit more material from the top edges. I also trimmed more material from the top and bottom of the belt so the belt boxes are pretty much aligned with the top and bottom edge. I used my Dremel to cut the slots into the belt buckle and the drop boxes. These are a little bit less than 1.5" wide, due to the forming of the pieces and not wanting to cut into the sides too much. Works out fine as the webbing fits snugly in the slot. I attached the white nylon webbing which forms the belt strap, to the plastic part of the belt. I did this by wrapping the webbing around my waist (with the flight suit on) to get the size right, then adding 6" length on each end for some slop. I then cut the webbing in half and glued it into the belt, avoiding the back of the buckle because that's where the other strapping will need to come through. E6000 as usual. Once that dried I tried it on again, marking with a pencil where it fell in the middle of my back. Once I knew this point, I could then trim the excess material off the edges and install the velcro. I trimmed and then sewed on velcro to the back side, approximately a 4" wide strip, making sure it would be covered by the thermal detonator. Once that was done I installed the 1/8" rivets. These should be installed from the front side of the belt with a washer on the back side. Simply drill a 1/8" hole through the webbing and the plastic and slip the rivet through. Then tried it on for size, aligning the bottom of the belt with bottom edge of the cummerbund. Early on in this process I realized I needed a way to keep the cummerbund from sagging. I glued velcro to the flight suit and cummerbund to hold this in position. Seems to work okay so far. Next I worked on the front drop box webbing and buckles. From the reference image in ROTJ and Mando, the buckles hang approximately where the side of the cod piece meets the pants. For the drop box attachment I used 1.5" natural cotton webbing. This stuff is thick. It should be threaded through the buckle slots as shown and secured. Presume glue or sewing is fine, I sewed mine ensuring the back part of the strap was hidden behind the buckle. Note, the male portion of the buckle hangs from the belt buckle. The female portion comes up from the drop boxes. I cut them to an approximate length based on trying on the belt with these straps hanging down for placement. I used the clips which came with the parachute buckles to temporarily hold them in place inside the belt cover. Once I was happy with their placement, I marked the back side of the webbing with a pencil and glued them in place behind the belt box then sewed the parachute buckle loops closed. Note, once you cut this webbing, the ends may unravel. To stop this from happening I sewed a stich line along the cut edges. Next step is to do the long straps which run through the drop boxes. Again I cut this about 6" longer than I thought it would actually be. The pic below shows the right side drop box. Note the female buckle which ties into the male buckle hanging off the center of the belt. Other side is the same, just opposite. The webbing straps go through the drop box, and are twisted inside which helps keep the box from sliding around while still being adjustable. I again tried on this assembly, roughly marking where these webbing straps intersected the middle back side of my belt as that's where they need to attach. Once I had that it was time to install the snaps. In the pics below you can see that I used a leather punch to make holes in both straps, the snap will fit through here, tying the two straps together. The finished side of the snap will face outward. The receiving snap will be connected to the white webbing on the back of the belt. As I had already sewed on the velcro to the belt, I decided to attach the snap to a small piece of nylon webbing which will then be sewn to the belt webbing. here's the drop box assembly with the rear strapping secured in place by the snap. Note the long ends will be trimmed off when I try the assembly on again, see how the boxes lay, and then mark where the straps overlap each other. Here's the assembly before I trimmed the rear straps. Once marked, I cut the straps, sewing the cut edge to prevent fraying and then sewing the overlapping edges together for added strength. And the complete assembly (minus the TD). And trying it on. And with the completed armor so far. Haven't filled the pouches yet so they're kinda flat. The thermal detonator is next to tackle. This thing is so heavy but I'm gonna work with what I got. The end caps seem gigantic, I know they're supposed to be bigger than the gray tube but is this too big? It came from RS so I presume it's correct, just looks weird. Need to re-review how this thing goes together, have a vague memory of zip ties and some kind clips. -
I just attached my tank recently using a bracket. That method was recommended to me and it worked well. I left the indent on that circle. Can't tell one way or another from the screenshots is it is there or not. Look at my build photos. I also painted it white like the ROTJ, perhaps the idea is the color wore off over time on these remnant guys. Figure I can remove the white if it becomes a problem for approval. Sent from my SM-G960U using Tapatalk
-
Fragarock's Scout Build
fragarock replied to fragarock's topic in Scout Trooper: "The Mandalorian" WIP
Quick question before I get too much further into the ammo belt. The CRL says "webbing" for the belt and for the drop box hangers. Is this nylon webbing (thicker and not stretchy) or stretchy elastic webbing (like the black elastic used on the biceps? I think it's the nylon type but hard to tell from some photos. Thanks -
Fragarock's Scout Build
fragarock replied to fragarock's topic in Scout Trooper: "The Mandalorian" WIP
Hi, Could use some advice on trimming of the drop boxes. Here are pics of the boxes as they came from RS and pencil trim lines I added. I trimmed these down but do you think I should remove more plastic? Wondering about the top mostly. -
Fragarock's Scout Build
fragarock replied to fragarock's topic in Scout Trooper: "The Mandalorian" WIP
Happy Thanksgiving Troopers! Yesterday I did a bit more work, getting the tank striping done. Used an adhesive matte black vinyl sheet cut into strips. I saw a few different thicknesses on others WIPs, I ended up eyeballing it a bit with stripes between 2mm-3mm wide. Eyeballed the placement as well. Hopefully it looks okay. While I await the arrival of some black sew-on velcro to attach to my flight suit, figured I'd get to work on the ammo belt. This thing is really wonky, not sure if this is how RS sends all these out but mine was bent all over the place and pre-trimmed.....over trimmed in some areas above and below the boxes. So, I cleaned up the top and bottom, leaving just about 1/8" or less over and under the boxes. I also heated this with my heat gun to get it bent around my waste properly. Based on the reference Mando images, where the trooper has his belt over the cummerbund pouches, the end boxes of the belt should be directly at your sides. Once I bent my belt, it seems to align in the same manner. Here you can see the overall ammo belt alignment. Wonder if this was an intentional costume choice or someone messed up when dressing him. I was going to start the main belt strapping but realized I only have 1.5" webbing, and it seems too thin so I ordered 2". Should be here Saturday and then I can proceed. On others WIPs I've seen some ABS reinforcement installed in the back side of the boxes. My ABS is really thick and I don't think I need to do that. Is there another reason people have done this that I may be missing? I'll have to hit the local hardware store tomorrow to get some washers for the rivets on the end of the belt, don't want them pulling out of the nylon webbing. Here's the cummerbund. Made by Kripton on Etsy. Fits perfectly as far as I can tell so far. The pouches are attached with Velcro and are removeable. I attached the loose end of the strap to the top inside area of the cummerbund. Again, it fits fairly well but I may need to tighten it a bit as I get further along in the build. Even came with additional sewn in velcro on the sides, presumably to help hold this in place on the flight suit. That's definitely going to be needed and I'll add more velcro in the front for support. From what I've noticed, the ammo belt bottom should align with the bottom of the cummerbund, so a semi-permanent attachment to the flight suit is a must. First try-on of this piece, sitting too low, will need to skootch it up a bit so the ammo belt will actually align with my waist. Should the cod fabric be pulled tighter, is it too low? Generally the crotch in the flight suit is way too low, I don't want to deal with the hassle of getting it re-tailored so I'm hoping I can just tighten up the back strap on the cod, pulling it tighter. The bunching in the pants is bugging me too, the legs are really big for my skinny limbs. As I work on the belt and have taken notes, I have a question about the back parachute buckles. Does the elastic simply get threaded through and over the top of the buckle? Is it not really secured to the buckle? Seems like the buckle could slide around. The photo below is from Christina's excellent build. Thanks! -
Fragarock's Scout Build
fragarock replied to fragarock's topic in Scout Trooper: "The Mandalorian" WIP
Thanks for the input, I'll work on getting some velcro attached to the flight suit and the biceps and forearms, I like that idea. Random question, the back strap for the cod piece, what is it supposed to attach to? The belt? -
Fragarock's Scout Build
fragarock replied to fragarock's topic in Scout Trooper: "The Mandalorian" WIP
So almost a month has gone by and during that time I've been working on the armor when I had time. It's been busy at work, Halloween birthday planning and kids sports. I've been tinkering, making adjustments, finding out what doesn't work and fixing things. Based on Chopper's input I went back to the tank and made some adjustments to the bottom so that it will fit better against the back. I did additional trimming on the sides to make this piece sit closer. I created a shelf bracket for the tank to sit on. Scrap piece of ABS clamped into my vice, heated with a heat gun and bent over. This piece was glued to the back with E6000, using magnets to hold it in place. Prior to mounting this I placed the tank in position and marked a pencil line where the top of the tank should sit then set the bracket slightly below that line. I thank prepared the strapping to hold the bottom of the tank in position. I decided to to internal straps on the sides and one on the bottom to be sure the tank wouldn't come loose. These straps have Velcro sewn on so they are adjustable and can be pulled really tight. Probably overkill but I wanted to be sure this would hold. I cut slots into the back armor and glued the Velcro/straps to the inside of the tank. Next I prepped the tank topper to be attached to the tank. Previously I'd painted the topper in matte black using an airbrush then applied several layers of matte finish clearcoat. I painted the white circle and the red stripe using Model Master Insignia Red. The white was their generic white which happened to be available at the hobby shop. I drilled a hole in the topper where the rivet would be inserted then glued the topper down to the tank. Make sure you use a rivet that is long enough to go through the topper and down into the bracket below. Set the tank atop the bracket and mark the hole location onto the bracket below. Here's the attached tank. And the chest/back assembly. Next I trimmed the shoulder bells along the pre-marked lines that came from RS. Added the elastic strapping at the bottom of the bells, but up high enough from the bottom to allow me to trim off excess which I was sure would be needed. These pieces are really wide when viewed from the side, to match up with my smaller frame I heated them up and bent them so the were a tighter curve and less wide. here's the comparison between the original shoulder and the heat bent one. Now, from looking at the reference photos from ROTJ and the Mandalorian, it was clear the stunt actors were fairly tall, certainly a lot taller then my 5'-5" frame. Because of their height and longer limbs, the armor pieces are more spread out, revealing the black flight suit below. I'd have to do some trimming to make my armor fit me better, like I did with my TK, scaling the pieces down where I could. The chest and back were sitting too low on my chest. I'm short and also have a spinal curvature which complicates the way chest pieces sit on me. So to fix this, as much as I could, I trimmed the top ends of both the back and chest straps, taking about 1.5" of material out in total. This would bring the chest and back up a bit, closer and tighter under my arm pits, closer to the look in the reference photos. Here's the tighter version after trimming. Once I felt the chest/back re-sizing was completed, I tackled the strapping. I decided to permanently strap the top of the chest and back together, rather than leaving the right side open with a snap closure. I can still get my head through the opening and the permanent glued straps on both sides hold the pieces together they way I wanted them to fit. The connection is made from elastic strapping with a snap sewn in the middle to receive the shoulder bell. For the shoulder bells I used the same materials, elastic and snaps. In this photo the two on the left are the chest/back connectors. The others are the should straps. I did a quick mockup to decide how much a gap should exist between the top of the shoulder and the chest, settling on 3/4". In the photo below you can see the bottom of the bell is too low. I'm gonna have to trim it to make the whole thing smaller otherwise the bicep will be crammed in there on my arm, smashing into the shoulder bell. So I trimmed off about 1/2 inch but it still wasn't enough. Before I trimmed anymore I figured I'd better make the biceps and see how they fit. Glued on the greeblies. When I first tried them on I realized the strapping was way too loose so I peeled it back and reglued it tighter. Then I was on a roll and made the forearms. Let me know if I need to remove more material from the top and bottom, seems a bit thick to me but I'm not sure. I also had to heat bend the forearms to fit around my skinny arms. Here you can see the trim lines before I cut. Original width of these was 5.5". When I was done heat bending them it was 4.5". So, I then tried all the pieces on again. I think the shoulders are good now. I trimmed a bit more off them and took 3/4" off the top of the biceps to make more room for these to fit on my arm. In the photo below the bicep is sagging. Can I used Velcro underneath the bicep, sewn to the flight suit to help hold this in place? Also wondering what's the proper placement of the forearm. In some ROTJ photos it appears high up on the forearm, strap running over the glove as seen in the photo below. In the Mandalorian it's above the glove, presume this is due to shorter gloves being used. Generally I presume it should be up high, right at the bend in the elbow, the uppermost part/top of the forearm armor actually resting above the elbow. Not sure is there's a hard rule about this as the bicep and forearms seem to be all over the place in various reference images. As I move forward I'll need to do the tank striping. Have the adhesive vinyl, just need to cut it out and affix it. Will make tweaks to the biceps and forearm placement based on any comments I get back. I did get my cummerbund althoug haven't opened it yet. Probably need to see how that piece fits in the overall scheme then jump into the belt assembly. Thinking down the road, may have to tailor the flight suit, it seems awfully baggy in the arms and legs. We'll see how the overall look develops as I get more done. Thanks! -
Fragarock's Scout Build
fragarock replied to fragarock's topic in Scout Trooper: "The Mandalorian" WIP
Thanks for the answers. I'm working on the bottom of the tank to tighten that up and get it attached to the back. I presume the pop rivet at the top of the tank is mostly decoration and the top plate can be glued down. Sent from my SM-G960U using Tapatalk -
Fragarock's Scout Build
fragarock replied to fragarock's topic in Scout Trooper: "The Mandalorian" WIP
I figured I'd tackle the chest and back assembly first. Get this biggest part out of the way first. Here's the chest piece as it came out of the box. RS guys trimmed it pretty well. I looked at reference photos and asked if there were known dimensions for the return edges which I should adhere to. There aren't so I sketched a line that looked reasonably close to the reference images, approximately 8mm although it tapers down in some spots. For reference, here's the bottom edge of the chest which I did trim down a bit by approximately 10mm. Here's the side of the chest, where the white straps go through. Again, drew a rough trim line. Basic trimming then ensued. Cut off the large strips that I could get to with the lexan curved scissors which I think everyone uses. Once I have the main cutting done I fine tune using a sanding drum on my Dremel which gives good control, but makes a mess. I then cut in the slots for the side strapping which ties the chest to the back along the sides. Again used the Dremel but with a sanding disc. Then cleaned up the opening with some sandpaper. I noticed that it's not plausible to cut a truly 1.5" long slice for the 1.5" strapping. The cut is smaller so the strapping will be taught as it goes through the opening. For some reason I forgot to take pics of the back piece during the trimming process. Just have this bottom shot. I taped the bridges of the chest and back together and tried this on for a rough fit. I found there to be a sizeable gap between my body and the upper part of the chest/back, at the bridges. So to reduce this I took some material off the bridges at both the chest and back. Most of the material was cut out of the back piece. About 1/2 inch out of the chest bridge shown below. I'm waiting on new Velcro to be delivered, once I have that I can build out the lower white elastic strapping and test fit this again over the flight suit. Then make additional adjustments if needed. Next I trimmed the tank. The piece had good pull lines which is where you see the pencil lines in these photos. First thing I did was mark a centerline down the middle of the back and another one down the tank to help align the two pieces. Then I started off trimming along these lines, then slowly refined the trimming. First I trimmed the top of the tank to get the profile to match up with the back profile. Then it trimmed each side, slowly removing more and more plastic to get it to match up with the back profile. I think I moved the side notch at least 4 times during this process. The bottom of the tank was the last thing I trimmed down to a rounded profile. I think my trim lines are pretty good and the gaps you see will go away once I mount the tank to the back. I know the screen used kits had massive gaps so I think what I have is good. What do you guys think? Here is the trimmed tank loosely set atop the back piece. The very bottom of the tank isn't going to get any tighter to the back without some heat forming. Below you'll see the resin cast greeblies from RS. I'll sand these down a bit. I'm confused by the knobs. One is tall and one is short. Which goes into the large piece at the top of the tank and then what is the other one for....thermal detonator? Also, are there specific colors for these parts? Specific black, matte, semi gloss or gloss? What about the red stripe? Here are the others. Pretty good detail in the casting. ROTJ costume for reference. Any specific requirements for this rivet and washer? ROTJ in the first image, Mandalorian in the second. Finally, my boots arrived! These are from Crowprops. They are slightly big because they don't normally make a boot to fit my smaller US 7.5 size foot. So I had to go with the US size 8 equivalent which will be fine, just wear thicker socks. Boot construction seems solid enough. There's even a nice little reinforcing band inside the right boot to wrap around your leg. Presume this is to handle the weight of the holster/blaster on the boot, keeping it from sagging. Flight suit bunches up a bit at the top of the boot. Maybe I'll add some straps on the bottom of the legs to hold them down, I'll figure out something. That's it for tonight. I'll keep working on the tank greeblies and mounting brackets to attach it to the back piece. -
Fragarock's Scout Build
fragarock replied to fragarock's topic in Scout Trooper: "The Mandalorian" WIP
Right on man. Thanks for the clarification. I see some folks have riveted, or glued the top, even used magnets. I presume a similar approach could be used to secure the bottom of the tank. Or maybe some kind of elastic strapping might do the trick, something that could be glued to the inside of the lower tank and pulled through into the back. I trimmed the chest and back, cut the slits for the white strapping at the bottom/side of the pieces. Also did a rough test fit using some tape to hold the bridges together and that led to a bit more trimming. Can't do much more until my black strapping for the bridges comes in along with some more snaps. Wondering about the logistics of putting on the chest/back pieces. Are people putting these over their head and securing the shoulders, then tightening up the white elastic on the sides? Started rough trimming of the tank as well. May work on the shaping/fitting of it so it fits nicely against the back some time tomorrow after my son's soccer tournament. I'll post some pics as well, once my phone recharges. Thanks again for the input. -
Fragarock's Scout Build
fragarock replied to fragarock's topic in Scout Trooper: "The Mandalorian" WIP
So, I have a question regarding the back tank. Looking at other builds it appears the tank is secured to the back with a strap extending out of the top and one out of the bottom of the tank, then around the back piece vertically. I'm not understanding exactly how this works or how the tank keeps from sliding around. Anyone have good photos showing how this was done? Thanks for the help. -
Fragarock's Scout Build
fragarock replied to fragarock's topic in Scout Trooper: "The Mandalorian" WIP
Tonight I'll start trimming! Big step to really get into this project and I'm excited! Here are a couple shots of the chest piece for reference. RS kit here. I can eyeball this but before I start trimming away, it would be good to know if there are specific dimensions for any of the return edges. Not just on the chest but the back as well, I'll tackle that next. Looking at the ROTJ reference photos there is a return edge and there is one on the actual chest piece I have. Eyeballing it, it may be in the 6-8mm range. The bottom part of the chest is a little harder to determine, not too many good shots of how that looked. It appears sizeable in the photos but my gut is telling me it needs a bit of trimming down, even if its just a 5mm. What do you think? -
Fragarock's Scout Build
fragarock replied to fragarock's topic in Scout Trooper: "The Mandalorian" WIP
I do appreciate the RS kit, super happy with my TK from long ago, held up and looks great. Quality cant be matched. Out of curiosity I did check on a WTF kit cost. Surprisingly its almost the same price as the RS kit but thats because I already had an RS helmet which would add significantly to the total cost (double the cost). And the Pound to Dollar exchange rate is favorable. Also about 8 weeks out for delivery which is too far out for me. Good suggestion though from you guys. I will likely make a new TD tube. The RS one makes me twitch just looking at it. We'll see once I get to that point. So far I'm just talking and haven't started any trimming. Sent from my SM-G960U using Tapatalk -
Fragarock's Scout Build
fragarock replied to fragarock's topic in Scout Trooper: "The Mandalorian" WIP
Thanks for the input and the history lesson. I didn't realize a WTF kit was used in the series but that explains the differences. I have to admit that I'm kinda wingin' it with this build compared to my TK where I did a lot more upfront research. So the additional insight is appreciated. Having but a TK and ST I'm confident I can make this RS kit look that way it's supposed to, just need to start which is usually the biggest obstacle. I'll continue to ask questions and again, appreciate the help. -
Fragarock's Scout Build
fragarock replied to fragarock's topic in Scout Trooper: "The Mandalorian" WIP
Today I got my armor from RS Propmasters. For anyone else who has this armor, I'm curious if you had the same issues I'll describe below. First some pics of the pieces. This ABS is off white in color just like my TK, typical for RS. But it's a bit more yellowey than the TK. Shouldn't matter since it's gonna get covered in muck. Some of these pieces seem really big. I don't know the average size of a stunt guy in the show but I'll have to do some trimming to get the pieces proportionally sized to my frame. Here's the shoulder bell which looks good from the front but will likely need to be trimmed and possibly heat bent to better fit the arm as it looks really wide. It's overlaid atop my TK for comparison. The TD chord piece is kinda weird. The RS piece appears to be some kind of sheet with grooves in it that is rolled around a tube, rather than a chord wrapped around a tube. Which is more screen accurate? The RS piece looks rough but I suppose much of it will be covered up anyways. It's completely rigid and I fear could break if dropped or bent in any way. Will that be a problem? I presume this piece should bend somewhat. They drew in pencil trim lines on some of these pieces. Not sure how they came up with them but doesn't look accurate to me. Perhaps it's accurate for the ROTJ armor but not even close to what is seen in the screenshots I have. Other than eyeballing it and making it look proportional to my smaller frame size, are they any known or required dimensions for these pieces? Similar issues with the forearms. Curious if this is something to cut to fit my size or if it must be a specific dimension. Any specific rules for where the elastic strap slit gets cut into the pieces? Also, the bicep and forearm appear to have a slight return edge which I'll have to replicate after trimming. Is this the case? Shoulder bells don't seem to have a return edge from what I see in the images. Any advice or tips is appreciated. Trying to look ahead and get questions answered before I start cutting into these pieces. I'll likely start with the chest/back pieces to set the overall proportions for the armor kit. Based on what I see, I'll probably have to heat bend the chest a bit as it looks really wide and flat across the front. I'll know better once I can rough trim it and mock it up while I have my flight suit on. -
Fragarock's Scout Build
fragarock replied to fragarock's topic in Scout Trooper: "The Mandalorian" WIP
Thanks. I'm pretty happy with it even though it took a while to get the process figured out. -
Fragarock's Scout Build
fragarock replied to fragarock's topic in Scout Trooper: "The Mandalorian" WIP
Hi Troopers! I've spent the past couple weeks working on my RS helmet repaint. I got this helmet last year and it was painted with a ROTJ paint scheme. Was never really happy with the paint job. I could tell they modeled it after a screen used paint job but it looked hokey. Maybe that's how the ROTJ bucket is supposed to look or maybe their paint job wasn't the best work, but I wasn't a fan. Doesn't matter any more because it's time to repaint! First I stripped off the old paint. Experimented with a couple if products from mineral spirits, enamel thinner and careful acetone use. Found that Testors Universal Enamel Thinner worked great. Dulled the shiny ABS finish a bit but that didn't matter and if you wanted that restore the shiny it could be done by re-polishing the helmet or spraying on a glossy clearcoat. For reference, here are shots of the original helmet and after I stripped it. Forgive the yellowish tone that from my basement photos. Looking at the screen captures and general color tone of the weathering, it appears there's a bit of grayish undercoating on the armor in some places. So my initial plan was to replicate this coloring as a base coat. I did numerous tests of acrylic paints, oil paints and weathering spray to work out the best way to do this. Generally I found that the paint coats would have to go down first with the weathering spray applied last. If that order is reversed, the liquid in the paints would wash away the weathering spray effect. So after multiple tests I decided to use the oil base paints which I got from my local art store. I used white with a touch of black to make a custom gray color. Maybe it was the specific paint I used but I had a hard time getting it to apply in a reasonably thin layer to the helmet while then being able to wipe it off. Wasn't as forgiving as the acrylics I used on my Shoretrooper. I tried thinning it with all kinds of stuff but found Naptha worked best making a nice thin liquidy paint. However the Naptha also acted as a drying agent speeding up the process which ultimately caused it's another problem. If anyone has a better suggestion for applying oils I'd like to know how to do it. I'll show what I did with this gray layer. Ultimately it was not successful and I stripped most of it away but something in this process may be useful for others. I applied the paint with a chip brush and then dabbed at the surface to get rid of the brush strokes and build up a grimy layer. The Naptha was really good at breaking down the paint so in areas I wanted to wipe it away, even it if had already dried, I dipped a paint brush in and basically erased the unwanted paint. Other nice thing about the Naptha is it didn't damage any of the decals on the helmet. I found wadding up a paper towel and getting that wet with Naptha worked well to remove some of the overall paint and start to create a weathered look of paint break down. Basically dab the damp paper towel on the surface until you get the look you want. After coating the entire helmet this is what it looked like. I immediately knew the coverage was too thick but thought I'd try to distress it and see what happened. To improve this condition, I hit it with steel wool to erode the finish and knock down the texture. The results weren't great and it took too long. So I decided to do a strategic wipe down with Naptha and a paper towel. This was the end product before I would apply the weathering spray. Next I applied the weathering spray. This is a product I used on my Shoretrooper and other props. Easy to apply and has a great effect if done correctly. Just takes a bit of practice. Here's the beginning of the application. You can spray it in multiple lighter coats or go heavy all at once. You'll get a different effect with each techniques. The idea here is to create a base coat of grime over the helmet which you can then distress and layer using multiple applications and weathering/distressing techniques. Areas that would naturally collect more dirt should be darker. You can see this in the screen used kit. Ear holes, recessed grooves, generally the sides of the helmet and front would be getting blasted with dirt while the back and top would have less exposure. In the image below you can see some whiter distress markings. This is done by applying a heavier spray to the helmet and immediately dabbing it with a paper towel, takes the color up in a nice fashion. One thing I happened upon was wiping a thin layer of Naptha over the dirt spray created this realistic crackled weathered effect, instantly aging the area. I continued this process all around the helmet and here's what it looked like. Later that night I started distressing this with steel wool, wire brush, files, etc. In the following photos the color looks a lot darker than it actually was, weird lighting I guess. While it looked okay. The color was really bothering me and I came to the conclusion is was the gray undertone. A bit too dark and to thick. So I went back to the Naptha and wiped away most of it. But I left some of the gray and initial dirt spray in place. Considered it an initial wear layer of grime to help build up the muck in certain areas. Here's after I removed most of the coating. The next day I hit it again with the dirt spray, this time with much better results and better technique from what I learned the previous day. Where the previous attempt was heavier and had the gray layer, this one was more strategically applied and more in line with the screen captures. I then reinstalled the lens using a hot glue gun which worked well. The following photos are of the completed helmet. After the final dirt spray application I dry brushed some raw umber into the ear holes to darken them a bit and a few other recessed areas. To lighten up some areas which were too dark from the spray I gently rubbed steel wool over the area which scraped away the coating in a uniform way. Other areas were hit with the heavier steel wool to add scratches and I used an emery board for smaller detail scratches around the snout and visor brim and to create a thin white border around the eye lens perimeter which was a detail I noticed in the screen captures. The scouts in the season 1 episodes had varying degrees of weathering. I went with the heavier version seen on the trooper who had Grogu in his bag. Here are some detail shots and a side by side of the screen capture helmet I referenced. May have to weather the snot a bit, too clean, maybe some darker oily kind of coloring. Here are the weathering items I used. #3 steel wool and #0000 which is the finer texture. This and the Naptha can be found at your local hardware store. Do not use the Naptha inside and chemical resistant gloves are a good idea. The Movie Magic dirt spray can be ordered online from various vendors. If in the UK, it's equivalent is called Dirty Down. The dirt spray can be wiped off of plastic with a wet rag pretty easily but on the ABS it became relatively permanent quickly, perhaps because I had already made the surface rough from various paint coats and chemical stripping. On smooth ABS it will take a day or two to dry but could still be removed. A clearcoat is recommended. In my case I won't need it. Good news is my RS kit has shipped! Not sure when it will arrive but likely in 7-10 days. Then I can get to work on the rest of this armor. -
Fragarock's Scout Build
fragarock replied to fragarock's topic in Scout Trooper: "The Mandalorian" WIP
Thanks. When I received it, it looked like a recast of the Hyperfirm but I don't want to say for sure, maybe just close modeling. I miss Hyperfirm, have an E-11 which is incredible. Wish I would have got my hands on more before they went under. The casting was so good. Sent from my SM-G960U using Tapatalk -
Fragarock's Scout Build
fragarock replied to fragarock's topic in Scout Trooper: "The Mandalorian" WIP
Good Evening, I got my blaster last week. It's a B grade model so it's a little rough but will do the trick. This is a cast rubber version so it will be durable for trooping, don't have to worry about dropping it and has a nice weight to it. Here is the paint job out of the box. Not bad but overdone for my tastes and doesn't match the screen used versions which were mostly shiny black with minimal distressin/scratches. I primed the blaster then started painting it with Alklad gun metal through my airbrush which gives a nice dark grey metal color. Then I I gave it some darker areas again with the airbrush and a darker color. Last paint was a bit of gloss black to darken the whole thing, although not applied in an opaque manner, a light mist so the bottom tones were still visible. Next I used some powdered graphite to give some areas a bit of a metallic shine, mostly in areas where finish wear would occur. This all got a semi-gloss clearcoat to protect the finish. Finally I did some scratches and metallic wear areas using Ak True Metal paints and a dry brush technique. Here's the final, simplified paint job with a bit of weathering and wear. I will likely drill out the fake screws and replace them with the real deal, maybe this weekend. Pictures make it look darker than it actually is. Here are reference photos of a screen used blaster.