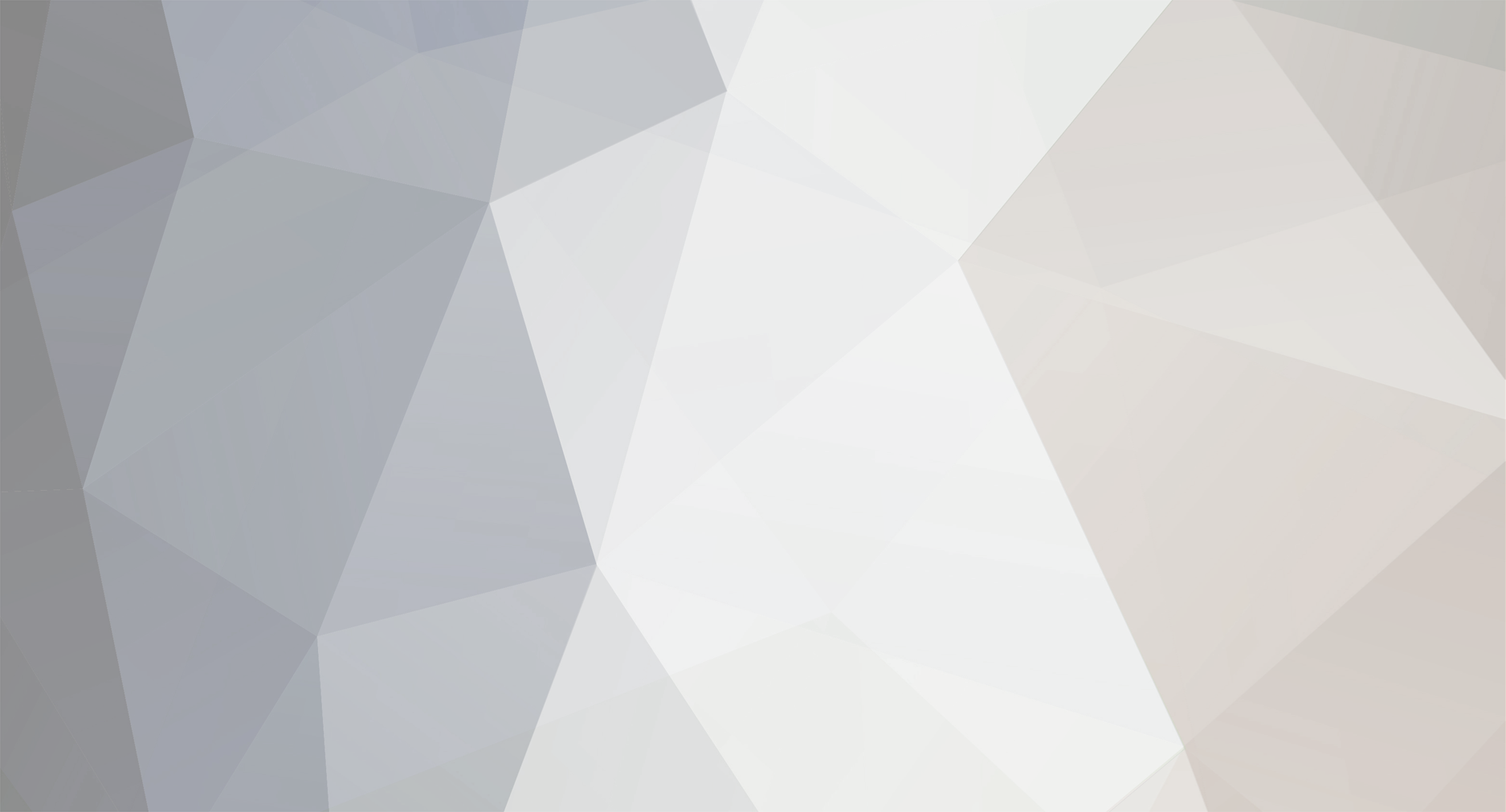
fragarock
501st Pathfinder-
Posts
67 -
Joined
-
Last visited
-
Days Won
2
Everything posted by fragarock
-
Fragarock's Scout Build
fragarock replied to fragarock's topic in Scout Trooper: "The Mandalorian" WIP
Thank you. I was really trying to match the screen look but with a different technique than others have used and one that I’m more familiar with from my shoretrooper build. Sent from my iPhone using Tapatalk -
Thanks Guys. I'm super stoked about this!
-
To get the armor kicked off I got a Creality CR-10S which has a print bed of 300x300x300mm or about 12x12x12". This was big enough to print the largest piece of the helmet. Took a bit of tinkering to get the thing figured out but after months of messing with it I threw away the print bed that came in the box and replaced it with a 12x12 mirror from Home Depot. I use Sticky Bedz adhesive spray which I leave on the print bed for multiple prints before cleaning it off with 91% isopropyl rubbing alcohol in a spray bottle. First thing to print as the helmet. Files are from Nico Henderson and they are excellent. Typically I printed with 4 walls and about 35% infill and a 0.15mm layer height. The snout which has much finer detail was printed with a lower layer height and a much slower speed. Printed in ABS. Here the print file setups so you can see how they fit on the print bed and their orientation. BP1. Outer blast plate took 27 hours. BP2 Faceplate. Printed at an angle so that it was mostly vertical, reducing the need for supports. Neck ring. This was the first really big part printed which took about 1.5 days. No supports needed other than what's shown in blue. Had to print this twice. Learned a hard lesson when priming this piece and left it in direct sunlight for too long. When I went back to check on it, the heat had softened and warped the piece so it had to go in the trash. Vents printed at about 0.5mm layer height. Snout. First time I printed this I had it flat on the print bed but didn't like the final look of the layers which came out quite visible despite being a low height and would be difficult to sand. So after a couple tries I determined tilting it at a slight angle produced better results on the top (front) of the piece. Base. This took about 6 days to print. Note that no internal supports are needed to support the top of the dome. I didn't believe it until it finished but I've printed this twice and not needed internal supports other than what is shown in blue. Here are a few shots of the printed pieces. Note that the first time I printed the face I printed both versions, one with eye bags and one without. Down the road I had to break out and replace the piece in the helmet with the non-eye bag version to fit the lens which Paul Prentice made. Here's the helmet during sanding process. Sanding was 80, 100, 200, 400 grit followed by filler primer. Then wet sanded the filler primer with 150, 200, 400 grit. Low spots in the print which couldn't be filled with primer were filled with Bondo glazing putty.
-
For my E-22 rifle I went with a 3D printed version from Eelco who has a print shop https://www.3d-props.com/. At the time he was printing and assembling his kits and you could even order a completely built/painted rifle. I don't think he does that anymore, only offerinf 3D files which appear to be similar to the ones I got years ago. He also has great photos of the blasters in their finished form. I recently got his files for a scout blaster and they were great. If you order 3D files you'll likely need to get the mounting screws and aluminum pipes which run through the rifle for support. This was the first 3D printed thing I ever had, so it was a learning curve figuring out how to finish it. The final work wasn't as good or refined as my 3D printed armor would be much later on but it was acceptable for the time and once painted black the imperfections didn't matter too much. Here are the individual pieces as I started sorting them, figuring out how it went together. First step to finishing the rough prints was to sand each piece with sandpaper in finer and finer grits. 80, 100, 200, 400. Once sanded I primed the pieces with gray automotive filler primer which you can usually find at auto parts stores. Sand the primed pieces with 100, 200 and 400 grit but this time wet sanding to get the smoothes finish possible. Any larger holes in the print were filled with bondo and sanded before the primer. Once parts were smooth, they were assembled. Some pieces like the counter and scope were made up of smaller parts so it was easier to assemble these before the final black primer. Other parts were bigger and were final primed individually. Here's the final black primer over the rifle. Here's the counter before assembly. Once I had a few good coats of primer on this I then painted it in a semi-gloss black paint. Then I rub in a coating of powdered graphite which gives a nice gun metal look. Then a clearcoat of spray can sealer to seal in the graphite. To add metallic highlights and barrel weathering I used AK TrueMetal wax paints. These are metallic based paints which come in a tube and are applied usually with a dry-brush technique which allows for very light application of the paint. If you want more paint on the blaster just lightly brush on more. Can also rub it on with a rag or paper towel. These are available at hobbie stores or Amazon. You can find videos online showing how to apply them. Primarily use aluminum, steel and brass colors. The piece below is the mount where the tactical scope attaches. Scope sold separately. The front of the barrels had 3D printed faux bolts. I replaced these with real ones from the local hardware store. I typically do this on my blasters. Cut or drill out the faux bolt and E6000 glue in the new one. With the scope I like to make it a bit more realistic by adding real lenses. You'll have to drill or cut out the interior guts of the scope on the large end to make this work. The lenses are harvested from monocular scope which you can find on Amazon pretty cheaply. Broke it apart to get the pieces I needed. The outer retainment rings are from Bulldog44 a 501st member who makes blaster scopes/parts. The monocular is a 8x20 type for about $8. Ended up gluing the larger lens and housing into an inner part from the monocular scope so it would fit better within the large cavity of the scope. Actually filled that cavity with play-doh first as a means to hold it in place. Added real screws to the scope. Then gave it a bit of brass color from the AK wax paints. Another component is the tactical light mounted to the side of the E-22. This is a real light which I got from a company called Surefire. It was there M300C scout light. Brace yourself because it's pricy. Current version is about $360. This comes with a mounting clasp allowing it to be attached to he side of the blaster. The 3D files may have a printable version of this now, not sure though. This is what it looked like out of the box. I took sandpaper to it to roughen up the edges a bit. Another needed item is a tactical rifle sling, get the kind with swivel ends which screw into the 3D printed pieces (I also glued them). Here's the final product.
-
Hi Guys, Back in 2019 & 2020 I may have been the first person to build a Mr. Paul's 3D printed kit and had a lot of help directly from Paul as I went through the process. At that time most of the ST communication was occurring on the Shoretrooper Family Facebook page so that's where I documented my build. I'm going to recreate that build here for folks to reference as they complete their own kits. So, keep in mind this work is already done, ask questions as usual and hopefully this will be useful for future troopers. You can also go onto the Facebook page and search Frank Fraga to find the build pages there. First thing I did was order a helmet kit from Jim Tripon. That is a fiberglass kit and was a nice helmet but ultimately I decided to replace it with a screen accurate version when Nico Henderson published his 3D print files about a year later. Early on I acquired the Yugoslavian ammo pouch on Ebay and got some really good boots (not Orca Bay) on Amazon. The color of the boots was a bit off, too tan and also too clean. So I darkened them with brown shoe polish and let them dry for a couple days then kicked them around my backyard and driveway to ding them up. In this early stage I wasn't sure which ST variant I was going to build so I got the basic colors for each at my local art store which sells the correct graffiti paint by Montana Gold.
-
Fragarock's Scout Build
fragarock replied to fragarock's topic in Scout Trooper: "The Mandalorian" WIP
Hi Troopers, After fixing the missing gray color on my drop boxes and removing the vertical tabs from the "T" greeblies my kit got approved! I have approval from the GML, just needs to be plugged into the system and transmitted to the appropriate parties within the 501st. Thanks to all of you who chimed in when I had questions and to those others who had really great build threads to reference. I've already replaced the dog bone leather covers on my boots with ones that extend down to the sole. Hope to submit for Level 2 approval soon. -
Fragarock's Scout Build
fragarock replied to fragarock's topic in Scout Trooper: "The Mandalorian" WIP
I went ahead and fixed the strapping at the front of the belt where the drop boxes connect. I figured it was easy enough to do and seemed to be a pretty glaring goof on my part. I'm gonna remove the old stitching to clean it up a bit too. I'm also going to nip off those tabs on the "T" greeblie on the biceps. They seemed so perfectly formed I figured they must be there on purpose. Perhaps they're part of the casting process RS uses. One of them is broken off anyways. I do see them on other RS kits that were approved though. Edit - RS confirmed those vertical tabs are on the original "found part" used to make this piece and they were removed for the film. I also fixed the recess panel on the drop boxes which I forgot to paint gray. -
Fragarock's Scout Build
fragarock replied to fragarock's topic in Scout Trooper: "The Mandalorian" WIP
Whoa, I didn't realize that little detail. If its a problem I can fix it relatively easily. It is nice having them function, a little easier to position the cummerbund. Sent from my SM-G960U using Tapatalk -
Fragarock's Scout Build
fragarock replied to fragarock's topic in Scout Trooper: "The Mandalorian" WIP
Hi, I just submitted my photos for approval. Put the whole kit on 3 separate times today so I'm getting faster but man getting that side elastic on the chest fastened up is hard. Also need a better way to secure the pouches, they are way too easy to remove, it takes some effort but they could still get ripped off during a troop. Here are some of the final photos showing weathering on the other pieces. Thanks for watching! -
Fragarock's Scout Build
fragarock replied to fragarock's topic in Scout Trooper: "The Mandalorian" WIP
Ya, its the US equivalent. Sent from my SM-G960U using Tapatalk -
Fragarock's Scout Build
fragarock replied to fragarock's topic in Scout Trooper: "The Mandalorian" WIP
It's called Movie Paint dirt spray. I haven't found it locally here in Michigan so I've ordered it. There are several L.A. based movie supply places that carry it. One if called FilmTools. Sent from my SM-G960U using Tapatalk -
David Remnant Scout Build
fragarock replied to Ghost40's topic in Scout Trooper: "The Mandalorian" WIP
Congratulations Sent from my SM-G960U using Tapatalk -
This is great. Congratulations on your great kit. Sent from my SM-G960U using Tapatalk
-
Fragarock's Scout Build
fragarock replied to fragarock's topic in Scout Trooper: "The Mandalorian" WIP
So, guess I'm nearing the end of this build. Last thing to do is to weather my cummerbund. Here goes! Started off by dying it with earl gray tea. used 3 tea bags and submerged the whole thing for a couple minutes. Surprisingly it changed the color a lot in that short amount of time. Once dry I added weathering detail to the stitching areas at the front and on the cod piece. These areas didn't naturally darken from the tea. This detail was created using oil paints mixed with Naptha and applied with a small brush. Get the brush very wet and let the color soak in along the seam. I used a mixture of white with a bit of raw umber. The idea is to make a very light beige mix that is very diluted. I applied this in layers, building it up. Then I made a new batch of burnt umber which has more red in it, again pretty diluted, to add color variation and more dirt effect. Added some droplets by flicking water/paint off the brush onto the cloth. In addition to the seams I added color to edges of the cummerbund and along the top where you can imagine sweat would build up and along the top of the pouches. Similar approach was used on the pouches, figuring a lot of dirt would collect at the top and bottom. Make sure the weathering on the pouches in consistent with the cummerbund. Then I used the dirt spray to give it an overall grunge look and applied more paint mixture. Here's the final product. Needs to dry outside until the Naptha evaporates off. I didn't document the weathering for the remainder of the armor but it's the same as what I've shown previously. Hope to have my submission photos completed this weekend. -
David Remnant Scout Build
fragarock replied to Ghost40's topic in Scout Trooper: "The Mandalorian" WIP
Seeing this, I'm beginning to think that I too should have made my own boots. I'll be watching with great interest! -
Fragarock's Scout Build
fragarock replied to fragarock's topic in Scout Trooper: "The Mandalorian" WIP
Finally got some warmer weather here in Michigan, had a couple days in the 40's and 50's so I got to work on weathering the hard parts. I used the same techniques which worked well on my helmet way back when I started this many months ago. The basic process is to create an initial build up of color and muck then wear it away and repeat the process 1 or 2 more times until you get a realistic built-up layering effect. I'm using a dirt spray which applies just like spray paint. This can be put on light or heavy or built up in multiple passes. Naphtha splattered on using a toothbrush or lightly rubbed via paper towel reacts with the dirt spray and creates an aged/cracked surface. The dirt spray is easy to remove and scratch off for about 24-48 hours, after that it sets in and becomes more permanent but can be washed completely away using naphtha if you desire. After the first application I'll wipe away some of the color. Mostly with a very fine steel wool, pressing lightly and in a random patter, almost erasing the dirt. I'll then use a paper towel wet with naphtha to distress certain areas more heavily. Acetone can be used very sparingly to instantly remove all color in certain areas. The next day I apply more dirt spray and repeat the techniques. Once the overall color tone and wear pattern seems right I scratch it up with heavier steel wool, a wire brush, and an emery board for finer wearing patterns along the edges of the armor or where I want to highlight something. I started with the chest/back as that's the biggest piece and the one which should really be in line with the weathering on my helmet. The smaller pieces will follow this general pattern. Larger detail shots, forgive the orange color in these photos, my basement lights make the pieces look darker and browner/oranger than they really are. -
Fragarock's Scout Build
fragarock replied to fragarock's topic in Scout Trooper: "The Mandalorian" WIP
Here are photos of the 3D printed blaster which is now completed. I finished up prepping it, then gave it a brown primer coat....just what I had laying around. Then I painted it with a few coats of matte black. We had a weird couple days here in MI where it got into the 40's and 50's so painting was possible. Fabricated a steel trigger guard and added real screws. Trigger guard and screws set in place with E6000 which seems plenty strong to hold it together. Once dry I gave it a light coating of graphite to add a bit of depth to the finish. Didn't want to go for a full metallic look so I went easy on it. If you haven't done this before, you can rub powdered graphite onto black to give it a metallic looking finish. More you add and rub in, the shinier it gets. Once done I coated it with a matte varnish from Montana Gold, again leftover from my ST. Did a few paint distressing effects, dry brushed. Here are the final photos. Top is the cast rubber. Bottom is the 3D print. In photo below the 3D is on top. Neither is perfect but the 3D print is smaller and fits my hand better. The cast rubber has it's advantage of being droppable without breaking. Question. I presume the neck seal goes over the balaclava for a neat/clean appearance with nothing hanging out from under the helmet. Guess the next step is to start weathering the armor. I think it will be above freezing this coming week so I may get a chance to work on it. -
Fragarock's Scout Build
fragarock replied to fragarock's topic in Scout Trooper: "The Mandalorian" WIP
Getting one step closer. Holster is done. I went back to my blasters and started the process of adding a metal trigger guard to each. Here's the replacement work for the cast rubber version. I used a 3/4" wide x 1/8" thick piece of galvanized steel bar. Found this at my local hardware store. Cut it down and bent it by hand in a vice....with a little persuasion from a hammer. Key thing is to wear safety gear. I cut this with a Dremel saw with metal blade. Cut really well just made a lot of sparks so be careful. Could also use a metal hack saw but that would take a while. Ideally a band saw would have been the perfect tool but I don't have access to one. When bending this, make sure you have the piece squared up in the vice, if you bend it at an angle you're going to regret it, really hard to fix. Here's the new metal guard, compared to the rubber one. I would have liked to round off the corners but just don't have the tools to make that happen. To remove the rubber guard I used a Dremel cutting wheel and grinding wheel. The grinding wheel is good for removing the left over material on the body of the blaster. I found some embedded metal reinforcing inside which I cut out of the way. If you do this, wear a respirator. The grinding creates a fine dust which is not good to breathe. I removed enough material as possible while keeping the surface flat to receive the metal guard. Next I marked the holes in the metal guard, drilled them out and then countersunk for the screws. After this I primed the metal, painted it and put on a clearcoat to protect the paint. Then it was time to install. Drilled some holes into the body where the screws will go in. I got screws of matching size at the local hardware store. I filled these holes and coated the contact area with E6000, placed the new guard on top and put in the screws. Let it sit overnight and it's good to go. This is the replacement holster from Studio Creations. It came pre-built which worked out just fine. I glued a couple extra magnets into the slot where the outer holster piece slips in. Not fancy but the E6000 will hold well and it does the job. The blaster will now be held in place with these magnets and is still easy to get in and out of the holster. Time to attach this to the boot. I positioned the piece on the boot and marked the hole locations with a pencil. Then used my leather punch tool to make the holes. Make sure a clean hole is made through the outer and inner layer of the boot. Next pick a rivet that will be the correct thickness for the boot, the holster plastic and the plastic inner washer. Then install all four rivets. Note that this goes on the right leg, photos are in the mirror so they're reversed. I'm waiting for a piece of steel to arrive so I can make a new guard for the 3D printed blaster. That's the one I'll use for this costume. The rubber one will be a good backup or display. Other than that, I think I'm pretty much done except for the weathering. That will be tricky as I'm in Michigan and the cold weather may not cooperate with my weathering efforts but I'll do a test piece and see. -
Fragarock's Scout Build
fragarock replied to fragarock's topic in Scout Trooper: "The Mandalorian" WIP
I have the 3D printed blaster nearly completed, just need to bondo a couple holes before painting. Here are a few shots of it. It's definitely a bit narrower than the rubber one I bought and has a good feel to it. Also added some real screws to make it look more legit. I did finally get the new and larger holster from Studio Creations. I tried to fit this new 3D printed version into the RS holster but it wouldn't fit either. Maybe RS sizes theirs for the blaster they make.....although you can't buy it without commissioning a full kit build. Or they drew their trim lines wrong on the piece they sent me. Lesson learned is not to trust their trim lines, I should have cut it bigger and made sure the blaster would fit inside. The ABS on the SC holster is bright white where as the RS is their typical off-white color. Luckily it won't matter as the weathering will make this irrelevant. The SC holster is bigger than the RS and will fit the rubber and 3D printed blaster. Here are some photos, which do you think fits better? ROTJ reference photo below. The rubber one fits a more snug in the holster which could be helpful for keeping it in place. I think installing some magnets is needed no matter which blaster I use. -
Fragarock's Scout Build
fragarock replied to fragarock's topic in Scout Trooper: "The Mandalorian" WIP
Yep, just need to source flat bar material from a metal supplier or hardware store. -
Fragarock's Scout Build
fragarock replied to fragarock's topic in Scout Trooper: "The Mandalorian" WIP
While waiting for a new holster to arrive. Hopefully tomorrow is the day! I've started building a new baster, hoping this one will be smaller than the one I bought and fit in the RS holster which I already have. If not, the one from SC is supposed to be larger and may fit the other blaster. We'll see.. This blaster is 3D printed. Haven't fired up the printed in at least 1 1/2 years, since I did the shore trooper. Got it dialed in pretty quickly and printed these parts out in 4 or 5 days. These are from Eelco over at 3-props.com. That's where I got my E-22. I've spent the past few days hitting these with filler primer, sanding, some Bondo, more sanding. The usual 3D print routine. Now I'm starting to glue the pieces together then will paint. I also got the gray rectangle painted on the chest armor. Testor 1138 gloss gray. Paint within the flat area of the rectangle best you can. Gonna be covered with muck and grime anyways so not sweeting it. -
Fragarock's Scout Build
fragarock replied to fragarock's topic in Scout Trooper: "The Mandalorian" WIP
I ordered a larger holster from SC and I'm also going to print a smaller blaster. We'll see which one of these options I finish first! Below are the knee armor pieces. The left one is trimmed, the other not. I left the trim lines on one of them so you can get an idea how much material I took off. Once trimmed up, I put them in a boiling water bath to reshape them. They come super wide from the vacu former and need to be tightened up, especially on my skinny legs. Once they were reshaped I cut in the side slots for the elastic to go through. I used the same 1" black ribbed stuff that I used everywhere else. I added a Velcro strip down the center which aligns with a matching piece on the flight suit. This will hold the knee in place. I made it long so that it's adjustable up and down. Figured that would be important as I'm still tweeking the overall costume alignment and spacing between the various pieces. The other sideways piece is where the elastic strap attaches. Here I sewed Velcro onto the elastic straps. One for each knee. I positioned the velcor side first then slipped the other end through the slot. Put on my flight suit and tightened it up until it felt really snug. Then I marked the non-Velcro end with a pencil so I knew where it entered the slot on the side of the knee. Once I had this done for each knee, I then trimmed off any excess strapping and glued the loose end to the knee plastic. Here's the Velcro glued onto the flight suit in the area of the knees. Put just enough to allow for adjustment but not too much where it would be visible. I tried on the costume which is mostly complete except for fine tuning. Still need to add the gray paint details and do the weathering. Of course need to finish the holster too. Let me know if you see any obvious issues that I can fix now. A few things I want to adjust: 1. I'm going to add velcro to the back of the cloth belt so it will attach to the back of the cummerbund. May do this with a snap as well to prevent it from sagging. Need to think about this solution because it's already sagging without the TD being attached. 2. Need to tighten up the crotch strap. The white crotch piece hangs a bit too low and loose. This will help raise up the pants which are also kinda low, just the way they were made. 3. Considering taking the boots to a cobler and having the tops lowered 1" or 2". These look too tall for my short stature and I think having more black flight suit visible between the knee and top of boot will improve the look. 4. Need to fill the pouches, probably with furniture foam that I have left over from my TK build. What's the correct thickness for these pouches? 5. Need to make the slot on the right side of the chest bigger where the side strap comes through. It's impossible for me to tighten up that side when I have the chest on. Can someone verify my strap rigging is correct on this side? Strap comes from the inside, through the slot to the outside and folds backwards upon itself. -
Fragarock's Scout Build
fragarock replied to fragarock's topic in Scout Trooper: "The Mandalorian" WIP
This is super helpful Chopper, thanks for answering this for me. Now just have to figure out which way to proceed. -
Fragarock's Scout Build
fragarock replied to fragarock's topic in Scout Trooper: "The Mandalorian" WIP
So........ not sure how to solve this problem. I have the holster pieces trimmed and mocked up their installation. But there seems to be no way my blaster will fit within the holster in the same way as shown in the reference images. Those images show the entire blaster, including the side scope within the holster. Mine won't fit that way. Not sure if the blaster I have is made too wide or if the pieces i got from RS are too small....which seems unlikely. Only way this blaster is gonna fit in here is for the scope to be on the outside of the holster. Any suggestions? -
Fragarock's Scout Build
fragarock replied to fragarock's topic in Scout Trooper: "The Mandalorian" WIP
I'm working on my knee armor and should have it finished some time tomorrow. While glue is drying, I've shifted over to the holster and have some questions. The photos below are from Woobies ROTJ wip. The outer piece of the holster slots into the main piece attached to the boot. Appears that a slot is cut for the outer piece to slide into. Once it's in place is it glued? I presume so otherwise what keeps it from sliding out? Next question. These five slots, are they a specific length or spacing? I can wing it from the reference photos but I figured there may be specific dimensions from the top of the holster and specific spacing between the slots. Finally, the corner rivets. Any specific spacing from the edge or wing it? Figure I'll reinforce the attachment area on the inside of the boot too. Don't want the rivet to pop out. Thanks!