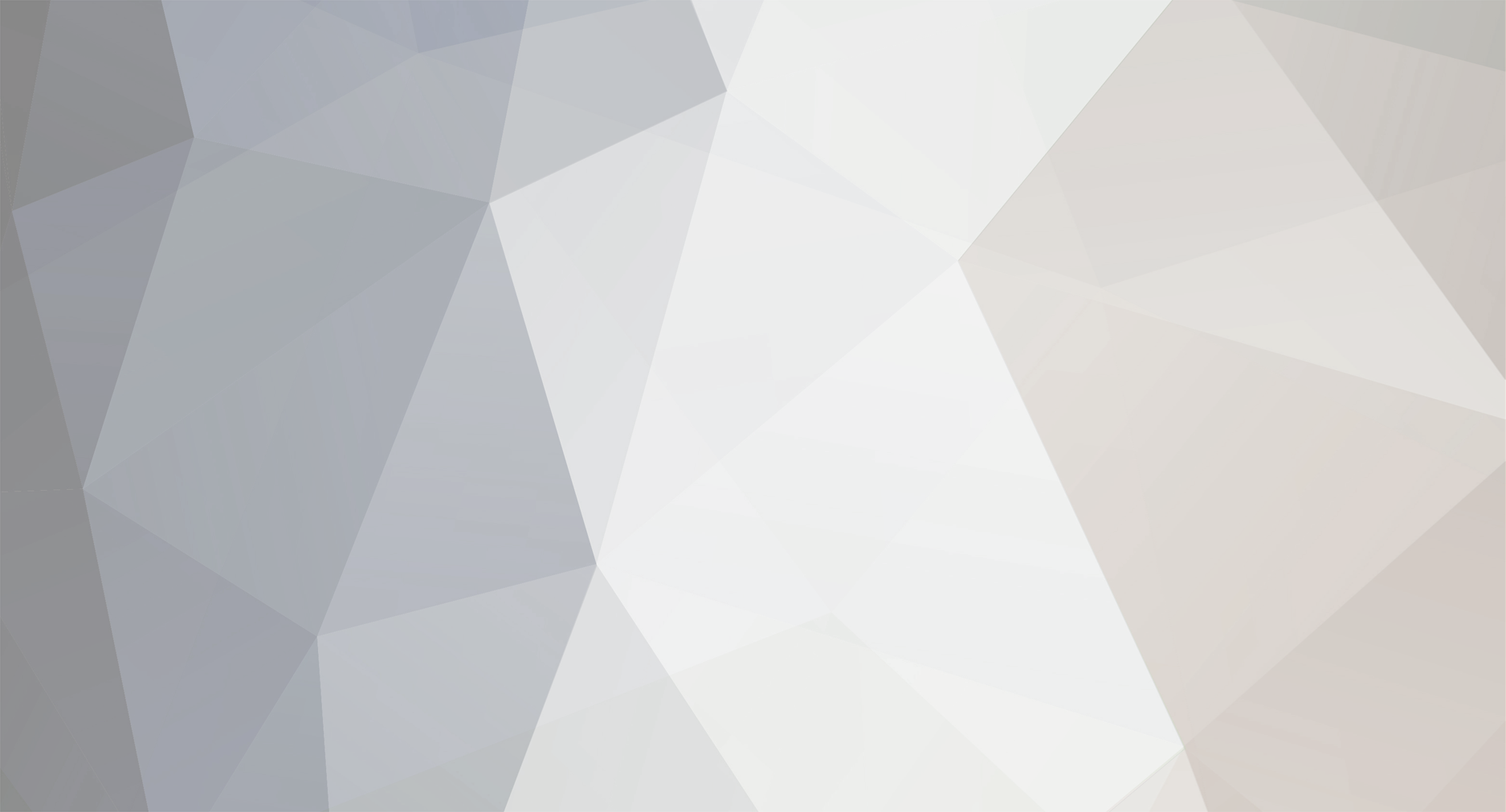
magicole
PFD Recruit-
Posts
8 -
Joined
-
Last visited
Reputation
15 GoodProfile Information
-
Gender
Male
-
Location
Salt Lake City, UT
501st Information
-
Name
Cole
Recent Profile Visitors
The recent visitors block is disabled and is not being shown to other users.
-
The belt and thermal detonator were fairly straight forward. Just had to dremel slots in everything and assembly with rivets. One warning I have to anyone wanting to do this is to put rivet backing plates/washers on any fabric surface a rivet touches, not just the "back" of a rivet. Here I only put a backing washer on the back side and the "face" of the rivet is already starting to pull through. For comparison, here's the other side where I did put a backing washer on the front as well as the back: Here's some photos of the finished belt and thermal detonator. I haven't picked up the clips to attach the detonator to the belt yet, but they are on my shopping list.
-
I took your advice and ended up getting a random hard hat liner from Amazon. https://www.amazon.com/gp/product/B00MH3XGCC It's a tight fit, but I think it will work. I ended up cutting/drilling a new hole to use the existing bolts in the helmet. Luckily the adjustment strap on the back fits perfectly into the bulge in the back of the helmet. The little metal tabs are supposed to fit into attachment points on a hard hat but they kept springing out and getting in the way when trying to fit it into the helmet. I just ended up zip tying those to the main band to keep them out of the way. I was wondering what the little white plastic tabs SC included with the helmet were for until I realized that they were for mounting the visor. The pre-bent piece fits perfectly in the nose to hold it in. Here's how I have mine mounted if anyone is curious. And here are a bunch of different angles of the helmet:
-
I've made a bit of progress while cooped up in my house but I'm just now getting around to posting it. I'll start off with the helmet. I'm using the SC helmet. Overall, I think it's a good helmet but it didn't fit together as nicely as I would eventually like. I think this is just due to the vacuum form process and the variance of each part. This helmet is great for now but I'm planning on eventually 3D printing a new helmet that fits together perfectly. I started off with the rear half of the helmet. All I did was scuff up the interface between the top and back parts and glued them together using the Shoe Goo from the boots. I used some small clamps to hold the two pieces together at the edges. While Shoe Goo may not be the best glue to use, it's been holding up well so far and I think it will give some flex if/when I drop the helmet. Next I cut out the ear holes. The Studio Creations kit comes with some good stickers for the ears but I wanted the ventilation of opening them up. I used the stickers as a template to trace cut lines onto the helmet, made a rough cut with the cut off disk of my dremel, then brought it out to the line with a sanding drum and needle files. Next was the front half. This is where I had the most issues with things fitting together. I started off by drilling a 1/8" / 3mm hole in the center of the bolt divots in the visor as well as at the small marks left in the plastic by the vacuum form mold in the face. I then bolted the two pieces together with some M3 bolts so I could get a feel of how it would look when assembled. There was some trimming I needed to do since the visor edge came up shorter than the face. After a lot of white dust from the dremel, things were more aligned. Next, I drilled some 3mm holes in the back half of the helmet to see the entire thing assembled. My first holes were way to far forward which left a big gap at the seam between the front and the back. The good thing about using small bolts for test fitting is that you have more leeway to try new locations. I ended up shaving a bunch of material off the "headband" of the front so that it wouldn't interfere with the dome. After a bunch of trial and error, I eventually got it to a point where the seam on the right hand side of the helmet was looking pretty good. For some reason, the left hand side of the helmet doesn't want to stay closed and has a big gap when the right hand side is flush. It looks good when I push it in though. I tried putting some velcro in there but I felt like I was going to break something when I undid the velcro. I'm thinking I'll end up putting some magnets on that edge so it can just slide open and closed. I then moved on to cutting out the eyes. SC marks the eye cut out line on the inside of the helmet which is really nice. Just like with the ear holes, I did a rough cut then expanded out to the line with a sanding drum. I ended up not going to the marked line in some places to keep the eyes as symmetric as I could. As that last image shows, I also masked out the snout to paint it with some black enamel paint. I also painted the "band" that goes from ear to ear of the back half of the helmet so that the ear holes look black from the outside. While I was painting, I hit the snout greeblie and ear bolts that came with the helmet with some Navy Aggressor Gray. The only thing left at this point was to expand the 3mm holes to ones that would accept the ear bolts, making sure to square out the holes in the front half of the helmet. After finally peeling off the protective plastic, adding the decals, and assembling everything together, I'm happy with the result. I still need to figure out padding though. Like I said before, I'll likely 3D print another one when I go for lancer status but this will work great for now. I'm realizing now that I don't have any other angles of the helmet, I'll get those when I post about the rest of the armor I've put together.
-
I ended up not sewing up the front pockets. My new seam line comes to just beneath the opening of the pockets so that they stay open. That's just where my reference pants ended so it seemed like a good spot. I'm thinking that my hip boxes/belt will end up covering the pockets so I didn't worry about it too much. Ask a way with any questions you have. I've been seriously impressed with how helpful everyone on this forum is.
-
Alright, I finally got the boots 99% done. The only thing I haven't done is cut out the top boxes on the heels. I'm waiting for a chisel tip x-acto blade to come in so I can get clean cuts. My dogbones are probably a little too short as they only reach to the toe banding on either side. I read somewhere that they should definitely not touch the sole so I erred on the side of caution. I ordered the SC armor and helmet kit last week as he was having a good "shelter in place" sale. It came in today (fantastic turn around time) so I'll start working on that when I get a chance. I took a guess at how tall the boots should be without having any knee armor. I might have to adjust them a bit depending on how the knees fit now that I have them.
-
Right. I was planning on leaving some up there but completely spaced drawing a line for it. Thanks.
-
Thanks for the tip. Looking at the CRL closer, I was actually already planning on doing a lot of the lancer requirements (like carving the boots and using real suede), I'll keep it in mind. Before I started carving up the boots I wanted to get some feedback on how the cut pattern looks so far.
-
Hi Everyone. This is my first project of this scale but I'm excited to get started. I'm doing a "parallel" build with Ditty, though we're starting off on different parts. Her WIP can be found here: I'm not going for Lancer status right off the bat but might eventually work up to it. I've decided to start off with the undersuit and the boots as they seemed like the easiest place to get started. I'll probably end up getting the SC armor as people seem to have had good luck with it. Undersuit: I got the Kolossus Deluxe Coveralls from Amazon: https://www.amazon.com/Kolossus-Cotton-Blend-Sleeve-Coverall/dp/B07BK8KRQ3. One thing I noticed before checking out was that there is are Deluxe and a Pro-Deluxe coverall that look nearly identical. The major difference I found was that the Pro-Deluxe has zippered chest and rear pockets as well as an arm pocket and a hammer loop. Make sure you get the Deluxe so you aren't having to remove extra zippers. I followed the advice from this post to use a pair of pants as a template to get the undersuit to fit better. I used a pair of 502 Levi's as the template. For the legs I ended up pulling them in 2.25" at the bottom and expanding up to 2" near the top. I then brought the seam to just beneath the pocket. For the arms I just used trial and error to end up with starting at 1" in at the cuff, going to 1.5" inches in 8" down the sleeve, then finally ending up 1" in about 2" from the armpit. I also removed the rear pockets and added the mandarin collar. Here is a before picture: and 3 after pictures: I'm going to try to get a start on the boots now. Hopefully I can finish one by the end of the weekend.