-
Posts
60 -
Joined
-
Last visited
Reputation
5 NeutralAbout silverBoyd
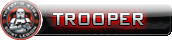
Profile Information
-
Gender
Male
-
Location
Charleston, SC
501st Information
-
Name
Jason
-
501st Designation
5945
-
501st Garrison
Carolina Garrison
-
501st Profile Page
http://www.501st.com/members/displaymember.php?userID=14658&costumeID=2
Recent Profile Visitors
The recent visitors block is disabled and is not being shown to other users.
-
Mountain Trooper Assembly (KB Props kit)
silverBoyd replied to silverBoyd's topic in Mountain Trooper WIP
There IS a rear cover plate. Similar to a Shoretrooper. Reread the CRL concerning the Thermal Detonator. For the Mountain Trooper, it states, "Thermal detonator is attached to a white plate the same height as the belt"...."There are 2 identical belt boxes mounted to the plate on either side of the thermal detonator, for a total of 4"..."The plate attaches to the belt in the rear, covering the belt closure". The rear belt plate was taken from the bottom of the rear lower torso armor supplied by KB Props. There is a line to cut. I used that as the rear cover plate to secure the TD to since it's already the proper width and shape. Two boxes will attach on either side of it as well. -
Mountain Trooper Assembly (KB Props kit)
silverBoyd replied to silverBoyd's topic in Mountain Trooper WIP
Thermal Detonator has been attached to Rear Belt cover plate. It was attached with (2) 1/4" x3/4" machine screws and Devcon Plastic Welder. After setting up overnight to cure, the Thermal Detonator is securely fastened and should stay on for quite some time. The Torso Armor / Chest / Back setup has been completed. The Rear Cover Plate that covers the zipper closure is held on with Industrial Strength Velcro. I opted not to use rare earth magnets here. In my experience, sometimes the simplest method is the best. I have Industrial Strength Velcro on some of my kits built 7+ years ago that is still going strong. This cover plate really locks into place once the Chest / Back Armor rests over it. Belt boxes have been trimmed and prepped for belt attachment. On the KB Props kit, 2 of the belt boxes and the belt buckle are 3D printed. Rather than using screw / post setup, I'm going to utilize the method that some use for attaching FOTK belt boxes. A simple setup of nylon webbing with holes punched in them. A thick rubber cord is then passed through the webbing. The ends of the nylon are secured to the rear of the boxes overnight with E6000 and magnets / clamps. **Remember to scuff the plastic with 80 grit sandpaper for the E6000 to make better contact between the nylon webbing and ASB** Be sure not to get E6000 on the center of the setup to allow for the cord to move. Holes will be punched into the belt fabric and the boxes can be tied onto the belt. Once you knot the cords, you can trim them and add a drop of super glue to the knot to help ensure they won't come undone in the future. The (2) rear belt boxes on both sides of Thermal Detonator have been attached. Two holes were drilled per box placement. I'm very pleased with how the setup turned out. -
Mountain Trooper Assembly (KB Props kit)
silverBoyd replied to silverBoyd's topic in Mountain Trooper WIP
The Chest / Back armor has been secured at the shoulders with a white canvas strap with (2) heavy duty snaps setup on each end (photo coming soon). Exterior rubber shoulder strapping has been glued down to the chest armor and the rear of the strapping has been attached to the back armor with white Industrial Strength Velcro to allow for ease of putting the armor on. The setup of the ribbed / rubber shin strapping has been setup. The rubber mat I used to make them was cut into 1.5" wide straps. I used a simple attachment utilizing Industrial Strength Velcro once again. The straps have been painted with 3-4 layers of gloss white paint. No matter what, the rubber had some kind of reaction and it dried more like an "off-white". I'm not sure what to do about that. Not sure there is much to do for it. The straps will be temporarily removed when I do the final paint on the armor. For this character, the shin straps do not go through the slotted buckles. They are installed behind them. The slotted buckles are for "looks". -
I'm currently painting a Mountain Trooper helmet right now. For the helmet....the CRL states the Frown is silver. That means the entire "frown" around the front of helmet correct? Also, on the snout....is it just the square and circular greeblies that are silver? On the action figure it looks like the entire snout is silver.
-
Mountain Trooper Assembly (KB Props kit)
silverBoyd replied to silverBoyd's topic in Mountain Trooper WIP
Turns out that the white Plasti-Dip has a strange reaction with the rubber mat that I cut into straps. No matter how many coats I apply, it turns a strange tan color. I won't be using that. Instead, I'll be using Gloss White - Rustoleum High Performance Professional Enamel spray paint. The same paint I'll be using on the helmet and armor pieces. It seems to be flexible and after 2-3 applications on the rubber straps looks great. See photo below (Top: Gloss White paint / Bottom: White Plasti-Dip) The buckles have been added to the shin plates. The strapping actually will fasten behind them and not through them which is odd. Forearm top greeblies cleaned up / primed / sanded and glued onto forearm armor. Center ab greeblie cleaned up / primed / sanded and glued onto ab armor. The helmet has been painted recently too... -
Mountain Trooper Assembly (KB Props kit)
silverBoyd replied to silverBoyd's topic in Mountain Trooper WIP
The helmet has had it's neck opening and eye openings cut out. Always the least fun part about doing resin helmets. So much dust. Defintielt make sure you wear a respirator or some type of mask when cutting / sanding resin casts. Cleanup of the surface continues... I spent a few hours prepping the surface and sanding down the areas of urethane resin that pooled up in some of the corners. Next, the helmet was given a soapy bath and then its first layer of Sandable / Filler Primer. After it cures all evening, the first full sanding will begin. After spraying the helmet gray, I can see a few spots that need a little attention. I have also done the work on the resin Thermal Detonator. One side of the TD needed to be cut off and sanded as flush as possible with 80 grit sandpaper on my palm sander. This was the side of the TD that was used for pouring into the mold. Next, the end cap on the TD needed some prep work as well. Once I was satisfied with the fit, I glued the two parts together with E6000 and it's being held together with tape overnight. The first stage of the rear zipper closure has been sewn. I still need to attach the soft Velcro and trim the length on this piece. I'm simultaneously building a Shoretrooper kit at the time of this build so this black zipper closure will be used for that kit. I will use white duck cloth and a white zipper for this Mountain Trooper kit. For the helmet lens, I will have to form the plastic to the shape of the helmet. I made a template with scrap Sintra. Used the heat gun to warm up the sheet of PVC board and formed it to the inside. This way, once I warm up the lens I can form it to this template for a better fit when the time comes. Helmet now has gone through some more cleanup and has received a second coat of primer. This time, Etching Primer. This coat will be wet sanded with 600 grit sandpaper. I finally sourced out a rubber strap for the shin plates. I found some 1/8" thick rubber mat with horizontal ribbing. The rubber is very flexible and should work perfect for this. I will spray them with 3-4 coats of white Plasti-Dip before attaching them to the backside of the shins with Industrial Strength Velcro. If the Plasti-Dip doesn't work I may have to try painting them white. With the size of the rubber mat I purchased, it could make a lot of straps in the future. This rubber material is the closest thing I could source out that was very similar to the First Order TK belt rubber that is used. The CRL only states vague details regarding the ribbed strapping so this should work fine. -
There isn't too much info on this type of armor yet so I thought that I would add my assembly for any future builders. This is not my personal kit. I am assembling this for someone else. The soft parts for this character are being handled by The Dark Side Closet I believe (tassets / pouches / boot gaiters). I will be looking at the 501st CRL along with many photos of the action figure to help assemble this. I have assembled countless armor kits, ranging from Stormtrooper's, Scouts, Animated Clones, Republic Commandos, FOTK's, TIE Pilots, and a few other types of armor so I am looking forward to getting my hands on a new style of armor. The armor / helmet kits are from KB Props. It has some great detail and nice pulls to the ABS plastic. The helmet is a great size too. Fits comfortably. Here's the rough-trimmed kit (below) after I have cut off all of the excess plastic that is on the parts when you receive your Big Brown Box. Not all pieces are shown in this photo. Since the helmet will obviously be painted, I will also be painting all of the white armor to match. For this, I prefer to use Rustoleum Professional High Performance Enamel - Gloss White. The red color on the Right shoulder bell I will be using Rustoleum Professional High Performance Enamel - Safety Red. Both of these paints have given me great high gloss results on many other armor kits in the past. The biceps / forearms / boot spats / shin armor / hand plates / shoulder bells / abdomen armor have all been assembled so far (see photos). ***minus a few greeblies attached*** Within the molded raised cover strips, on the biceps, I had to fill in the inside space with scrap ABS to be able to provide a better gluing surface (no pictures of that). This extra step made it easier when assembling the two halves together. FOTK-style forearms (rectangular greeblies still need to be attached to the tops) ***Unlike using these forearms for FOTK armor, on the Mountain Trooper, their forearms DO NOT have the clip greeblies on the side. Nor do they have any black detailing.*** Hand Plates have been trimmed and ready to be fastened to the back of a pair of gloves from Endor Finders. Shoulder Bells are trimmed and heavy duty snaps (not seen in photo) have been attached to the inside for connection to chest / back armor. FOTK-style Boot Spats are glued together and one end of the opening will receive Industrial Strength Velcro to hold them closed. Velcro will be applied after painting. ***Unlike using these spats for FOTK armor, for the Mountain Trooper, their boot spats DO NOT have the clip greeblies on the side*** Shin & Knee Plates have been attached to one another per the CRL to make them "one piece". I had to trim the knee armor in a way to rest on top of the shins. I permanently fastened them together utilizing DevCon Plastic Welder - Cream. The (8) rubber straps and strap slots still need to be attached. The chest / back armor has been trimmed, heavy duty snaps attached under the shoulders (not shown) and the rear back greeblie has been prepped and is ready to be attached. The molded area on the back armor that receives the rectangular greeblie is just a touch too small in the corners. The resin greeblie fits inside but it does not actually touch the bottom of the surface. After sanding and smoothing the surface of the greeblie I had to glue a rectangular piece of scrap ABS to the backside to be able to adhere it in place inside of the armor recess. I also had to carefully open up the corners in the recess areas to allow the greeblie to sit in as far as it could. ***forgot to take photo of this before I glued it into place*** As with all of my resin greeblies, before gluing them onto armor and painting them I like to give them a soapy wash to rid them of any mold releases that may still be on the surface. Once they dry, I will use Bondo brand Spot Putty Glazing to fill in small imperfections & sand with 120 grit. After that, spray them with a Sandable Filler Primer and sand once more with 180 grit. Finally, to ensure that the final paint will adhere properly to the resin parts, I will spray them with Etching Primer and wet sand with at least 600 grit. This gives the resin greeblies a smooth surface and a very nice finish to receive the final paint. Although all of the prepping / sanding is monotonous work, it will give you a much better final result in the end. The Lower Abdomen Armor was pretty simple to adhere together. I figured out the angle of the raised rectangle on the sides of the armor by taking a piece of paper and creasing it on the raised portion of the armor. I then cut the crease in the paper to make a template. This was then transferred onto the rear portion of the armor. I then trimmed the sides of the Lower Back armor to match this angle. It came out pretty exact. As always with assembling ABS armor, the surfaces to be glued together were roughened with 80 grit sandpaper and glued together with E6000. I left them held together with clamps & magnets overnight to ensure a strong bond. Since this armor will flex in this area that is why I prefer to use E6000 glue. I recommend leaving the rear portion of the lower torso armor in one piece when gluing the two halves together. I find it easier to assemble as one whole piece before you cut open the rear portion for proper sizing. Based on the measurements I am building this kit to, I will have to cut open the rear to fit the wearer. The rear opening will then utilize a custom-made zipper closure similar to what is used for some Shoretrooper armor. This will be closed off with the rear cover plate (not shown). Photos of this zipper closure coming soon... 2 of the 3 resin greeblies for the front Abdomen Armor have been cleaned up, prepped and attached. I made sure to sand the surface they were gluing to as well as the underside of the greeblies. A few years ago, I discovered a great glue called, Beacon brand Quick Grip (see photo below). I have nicknamed it "Greeblie Glue" because it's perfect for gluing on resin greeblies (big and small). It cures within 3-5 minutes and has a very strong bond like E6000 does. However, I would not assemble armor with it but it's fantastic for adhering small detail pieces. For the smaller front rectangular greeblie, I carefully warmed it up with my heat gun and formed it to the curved surface of the armor. After 2-3 tries, I was able to shape it so that I could get the maximum gluing surface. I'm happy with how it worked out. I still need to prep and glue on the front / center greeblie for the abdomen. This is as far as I've gotten so far. Currently I am custom-sewing the rear zipper closure. I will also begin work on cutting out the eyes and cleaning up the neck opening on the helmet.
-
thanks so much. Looks easy enough to make. Is that a zipper in the front?
-
any photos of the boot gaiters? did you make them or buy them?
-
curious what you used for the ribbed strapping on the shin armor? Any links as to where to find it?
-
are these 3D files something you have to pay for?
-
looks good. I haven't started on my trigger yet. Still working on carving out some details in the main body
-
no...they don't come in black. Only seen them in white. Thought about covering them ina thick layer of plasti-dip first. What you think about that?
-
I haven't documented my build on MEPD or CG forums yet but feel free to use any of my pix on here. This week I worked on my barrel. Drilled out holes on the template I made from scratch. Drilled out the holes utilizing a 3/8" diameter drill bit. I have an inner barrel too but haven't cut it yet. I'm planning on building my bipod from scratch using 12" shelf support brackets from (ClosteMaid brand) (http://www.homedepot...93?N=5yc1vZc89l) & 1" dowel rod pieces. I'll elaborate later.
-
finally finished a 2nd pair of Scout boots for a friend of mine. Also carved the soles for him too. I learned some tips since my first pair. Got the dogbone on the correct way this time too. The marine grade vinyl is pretty easy to work with overall. I think the hardest part is getting the vinyl stretched over the toes (front half of the boot). After that it's a breeze. I had to resize my templates in AutoCAD for this set since the first pair I made was a size 8 1/2 or something like that. These were for a size 10. Took me 3 tries to get it sized just right. Also had to scale the dogbone up from 10" across up to 10 1/4" to get a nicer look when placed on this boot. Even though I'm glad to be finished with them I'm actually kind of bummed to see these boots go.