-
Posts
125 -
Joined
-
Last visited
-
Days Won
2
troygordon2 last won the day on April 23 2021
troygordon2 had the most liked content!
Reputation
134 ExcellentAbout troygordon2
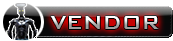
- Birthday August 8
Contact Methods
-
Facebook
facebook.com/lunaarmorworks
Profile Information
-
Gender
Male
-
Location
Montana, USA
-
Interests
Art/sculpting/3d modeling and printing, Snowboarding, xbox (Halo, PUBG, Ori, Battlefield 4, Skyrim)
501st Information
-
Name
Troy Gordon
-
501st Designation
22406
-
501st Garrison
Timberline
-
501st Profile Page
https://www.501st.com/members/displaymemberdetails.php?userID=33125
-
Approved Pathfinder Kits
Scout Trooper: ROTJ
Recent Profile Visitors
The recent visitors block is disabled and is not being shown to other users.
-
New Patrol Trooper Helmet Maker
troygordon2 replied to MrPoopie's topic in Patrol Trooper Armor/Helmet
I think I printed the original for finishing and molding based on the dimensions of a standard TK stormtrooper helmet. It's just too expensive to make so many different molds, though I wish I could get away with it! -
I'll PM you. Etsy is horribly difficult to work with lately.
-
Black Series Helmet - NOT APPROVABLE
troygordon2 replied to Donovan's topic in ROTJ Biker Scout Armor/Helmet
Again, I could have sworn the standard not long ago was "general shape." That's some good wiggle room for things like visor shape and dimensions. There was nothing about a "return edge" when I designed my helmet and got approved, which is now present. Am I'm no longer approved? "True to shape" should, at this level of specificity, now require the particular materials used, no? Dimensions at least? PLA at so and so mm thickness? There needs to be more detail now that this can of worms has been opened. We take scale into consideration when looking at approval, but looking over that Jesus Salmeron file, I'd say the angles on the face plate are FAR sharper than those used in the vac formed screen used props. It's not "true to shape." Never mind the hard edges I'm seeing in and around the ears. I think we owe it to everybody who is willing to put the time and effort in to be specific and exact. I personally find this frustrating as a maker, yes, but I expect a lot of people out there will wonder what else isn't "exact" about their build. The Hasbro helmet looks like garbage in my opinion. Fine for a shelf, a shred above Spirit Halloween, and inadequate for approval for a wide variety of reasons. The Salmeron helmet isn't much better in its current incarnation. I can't fathom the requirements for the EC-11 given the quality of the props used in filming... I recommend adding more details regarding that return edge comment to clear up any ambiguity on this. Perhaps "The visor is XX mm thickness throughout the entire component with a return edge on the face and gently curving bevel around the rear and hinge area where it meets the main body of the helmet," or something like that. Maybe there is no confusion in your mind, but there is in mine. This makes me suspect others in class don't want to raise their hands, so I'll speak up and take the talking to. -
Black Series Helmet - NOT APPROVABLE
troygordon2 replied to Donovan's topic in ROTJ Biker Scout Armor/Helmet
So, I saw this and felt it needed to be addressed. The 501st requirements are pretty clear about what needs to be done for approval, and right now the term "true to the shape of the original screen used helmet" is used to describe the design. I could swear that it was "general shape" very recently... I agree that things like the battery pack and inset vents defy that, but this return edge may require some specificity in the CRL. If the return edge needs to be present, what's the width? What's the sharpness? Why not say, "vac formed from XX width plastic?" As somebody who made his own helmet that isn't vac formed, this means I'm out of spec and no longer approved? I'm willing to bet that many others who made theirs with 3d printed designs are also now out of spec. Am I wrong on all of this? -
Black Series Helmet - NOT APPROVABLE
troygordon2 replied to Donovan's topic in ROTJ Biker Scout Armor/Helmet
As an artist, this news is absolutely disheartening. -
EC-17 Paint Question - Clear Coat
troygordon2 replied to DoubtFreezer's topic in ROTJ Biker Scout Weapons
I use matte paint when I paint mine and then coat with the semi gloss or flat coat. Even the flat has a sheen to it and it comes off looking rather like a genuine firearm finish. I have found, through quite a bit of headache, that gloss runs more and is harder for follow on coat to get a good grip on. Whichever way you go, hold the can a good distance away and take your time between applying layers. Slow is smooth, smooth is fast. Spray paint is deceptive in that it appears to be a great idea, but in reality it takes a long time to get it on right. -
Random thought from the Peanut Gallery: Put down the dremmel. It's tempting to think of it as the best tool, but ABS sheets are thin, will warp just from heat, and once that dremmel gets away, it causes all sorts of problems. I had a much easier time and required a lot less repair work by using an Xacto knife. Whittle away slivers at a time along your trace lines and then use some 120 grit or finer sand paper to smooth things out. Those ear holes are a pain in the butt, and I have to use a dremmel and oscillating saw when i finished the resin Scout helmets that I make and sell, but i've been doing it for a while now and (for the most part) have my technique well rehearsed. Even then, I can patch resin easier than ABS. Use power tools sparingly and you'll save yourself a ton of time on repairs. Remember, SLOW IS SMOOTH, SMOOTH IS FAST.
-
I make both, but I don't make the X scope portion of the DLT 19. I make them from resin too, so no print lines, and they don't be affected by heat and are much more durable. PM me if interested, I need to get back to work before the cold temps come back anyways.
-
Lens Material for Helmet?
troygordon2 replied to ItBelongsInAMuseum's topic in ROTJ Biker Scout Armor/Helmet
Man... The number of times I've trimmed those up for Scout helmets only to see that safety and corporate information written in the corner of the visor I intended to use... -
Fibreglass Armour Backing
troygordon2 replied to CaptainCunning's topic in Shoretrooper Armor/Helmet
Superglue seems to work best on a gel coat surface that's been lightly sanded. I had no problem getting the plastic or the fabric nylon strapping to stick. CA does not seem to like it as much for whatever reason. If you're putting in strapping, I'd recommend impregnating it in between layers of whatever material you decide to use rather than gluing. It will prove much stronger if buried. Doesn't hurt to cut small holes in the middle of the straps too to ensure a better adhesion above and below the strapping. -
Fibreglass Armour Backing
troygordon2 replied to CaptainCunning's topic in Shoretrooper Armor/Helmet
Again, I've only used it as a top coat and then backed it with something else. I can't think of a reason why glues wouldn't bond to it, just depends on the glue. It's a wonderful material, but as you said, a tad more expensive. I make most stuff by slush casting polyurethane resins, but occasionally do a gel coat. I'll give it a test later, I have some scrap, and see how good old super glue and CA do with a plastic part and some fabric on it. -
Fibreglass Armour Backing
troygordon2 replied to CaptainCunning's topic in Shoretrooper Armor/Helmet
I've used both gel coat and plastidip. On gel coat, it's excellent stuff, but make sure it will bind with the material. Don't think it should be a problem with any older fiberglass resin, but I've only ever applied the gel first to the mold and then resin backed fiberglass to it. Again, probably not an issue. Also, it's applied with a brush, and that's easy. On plastidip, people seem to love it, but I do not since it peels away. A better product may be pickup truck bed liner, which comes out thick from a spray can and is very tough stuff. I can't say I've ever seen it chip of peel. Sand and trim away the pokey stuff with an Xacto knife (or whatever) and clean away the dust before applying anything. And wear a respirator for all of the above. -
I make and sell a lot of different helmets, and my go to is a simple hot glue gun. DON'T use "All temp" glue though. You want the HOT stuff. Don't we all... Make sure it's hot or high temp glue though as the alltemp stuff does a poor job of holding on to plastics.
-
Which sellers have the best armor?
troygordon2 replied to ScoutsAreCool's topic in ROTJ Biker Scout HQ
I'm 6' 180, and the SC kit was excellent and shipped quick. No real reason I went with them over Moncal, but the Scout kit was available, the contact/customer service excellent, and the price fair. The plastics used are all very nice too. I recommend staying away from the Walt's Trooper Factory stuff. It's quite flimsy and has a poor reputation.